jeepcj3a
Well-Known Member
- Joined
- Jul 13, 2006
- Location
- winston salem
**Tig and plasma table update in last post**
Thought I would post in case it helped others and hopefully get some feedback as I learn how to weld. (Let me know if wrong section).
I last tried welding about a decade ago with a Hobart 140 mig but had to sell it not long after. Fast forward to now and I got a EMP215ic ESAB and am using .030 ESAB OK Aristorod, 75/25 gas, and their factory accessories. Finally hooked it up tonight to try it out. Helmet is the Sentinel and using a Miller respirator with P100 filters (snug fit under the hood).
Set up all per their guide, purged the lines, set at 20 cfm (18 when trigger pulled) and did a quick grind on the 1/8” wall tubing with my belt grinder.
Machine set on sMig which displays the voltage and amps as it adjusts it for you as you weld and displays the final setting(?) for a few seconds after you’re done. Results: (109A/21.2V read out for first and 107/24 for second):
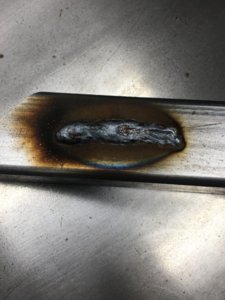
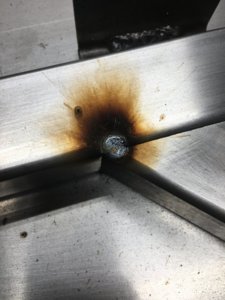
Then tried some clean 16ga, big mess with lots of porosity. Put everything up, bled the line and started watching YT videos to see what I was missing. Then remembered one video mentioning to make sure you fully seat your torch connector in the machine (and many of the comments on that video echoed that). Well I checked and mine was a little more than 1/4” out from being fully seated. Fully seated it, set machine back up and got the following on another piece of 1/8 wall. Gas back at 20cfm with 18 when trigger pulled. Some welds were brushed with steel brush in between. All welds had new wire snip.
(1st: 121A/19.5V; 2nd: 113/18; 3rd: 104/18.2; 4th: 117/18.5)
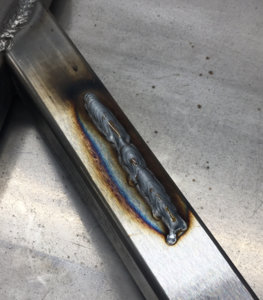
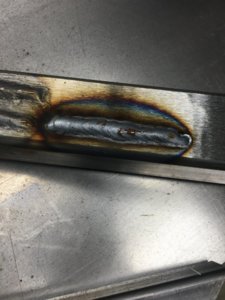
Profiles:
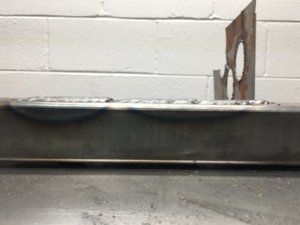
Last one I did, also shows a weld from when connector was leaking gas. (106A/18V)
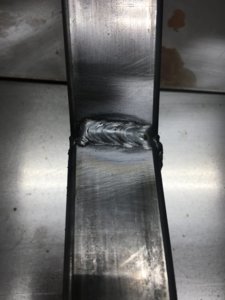
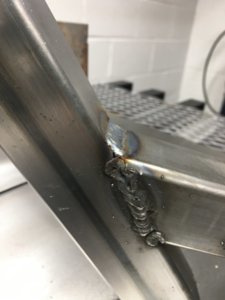
Ill be cutting up some 3/32 wall tube sections this week to practice and small squares of 16ga to try that again. Definitely need to work on distance that I am keeping the nozzle from work piece as I move my hands. Any suggestions on ways to improve would be greatly appreciated.
Edit: I was misreading the gauge. The figures above actually were L/min. It ends up I was at 42 CFH which was still in the gauages “Mig” zone but from what I have read that’s over double what it should be.
Thought I would post in case it helped others and hopefully get some feedback as I learn how to weld. (Let me know if wrong section).
I last tried welding about a decade ago with a Hobart 140 mig but had to sell it not long after. Fast forward to now and I got a EMP215ic ESAB and am using .030 ESAB OK Aristorod, 75/25 gas, and their factory accessories. Finally hooked it up tonight to try it out. Helmet is the Sentinel and using a Miller respirator with P100 filters (snug fit under the hood).
Set up all per their guide, purged the lines, set at 20 cfm (18 when trigger pulled) and did a quick grind on the 1/8” wall tubing with my belt grinder.
Machine set on sMig which displays the voltage and amps as it adjusts it for you as you weld and displays the final setting(?) for a few seconds after you’re done. Results: (109A/21.2V read out for first and 107/24 for second):
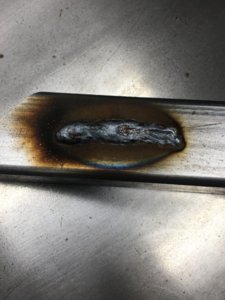
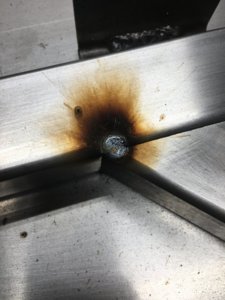
Then tried some clean 16ga, big mess with lots of porosity. Put everything up, bled the line and started watching YT videos to see what I was missing. Then remembered one video mentioning to make sure you fully seat your torch connector in the machine (and many of the comments on that video echoed that). Well I checked and mine was a little more than 1/4” out from being fully seated. Fully seated it, set machine back up and got the following on another piece of 1/8 wall. Gas back at 20cfm with 18 when trigger pulled. Some welds were brushed with steel brush in between. All welds had new wire snip.
(1st: 121A/19.5V; 2nd: 113/18; 3rd: 104/18.2; 4th: 117/18.5)
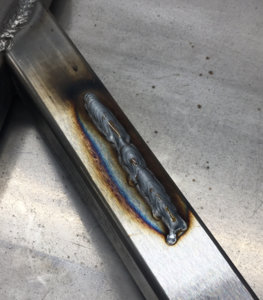
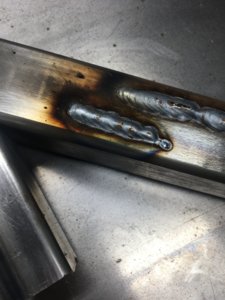

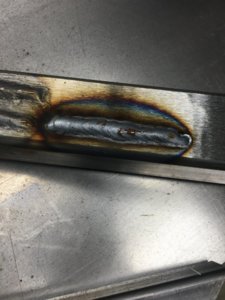
Profiles:
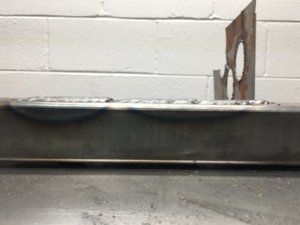
Last one I did, also shows a weld from when connector was leaking gas. (106A/18V)
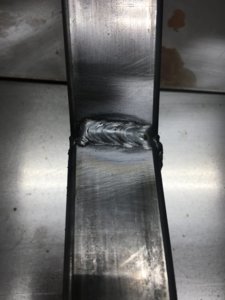
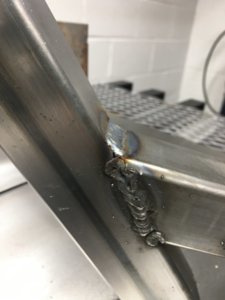
Ill be cutting up some 3/32 wall tube sections this week to practice and small squares of 16ga to try that again. Definitely need to work on distance that I am keeping the nozzle from work piece as I move my hands. Any suggestions on ways to improve would be greatly appreciated.
Edit: I was misreading the gauge. The figures above actually were L/min. It ends up I was at 42 CFH which was still in the gauages “Mig” zone but from what I have read that’s over double what it should be.
Last edited: