ponykilr
Guest
I loaded my welder with .024 Hobart wire today after reading all of the positive comments on it. I previously had used .030 and .035 mostly.
1-My thoughts:
2-It needs a lot more wire speed to look and sound good. About 30-40% more.
3-It is WAY easier to control/push the puddle. The puddle does not get in the way like with thicker wire.
4-The bead is prettier. It looks more professional, plain and simple.
5-You can move a little slower and watch it "burn in" or fuse because the puddle grows much slower.
6-Control, control, control.
7-It was hard to even try to make an undercut weld, my nemesis. It is worth using for this reason alone.
8-It did not really like my highest heat setting (140A) and tended to be more sporadic in the quality and ease of the weld. This might change on thicker steel or with more practice.
Overall, I like it and will continue to use it.
The side of these washers closer to the center was done with the .024, the other side (second pic) was with .035. Notice the thinner but much better bead on the first pic. These are small washers, the added control and smaller bead is a HUGE plus.
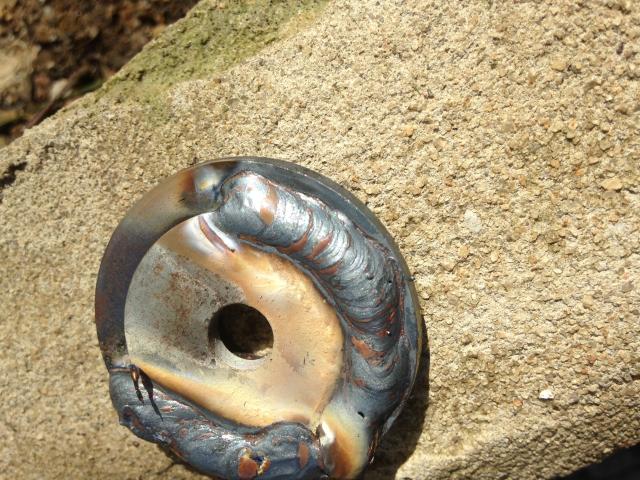
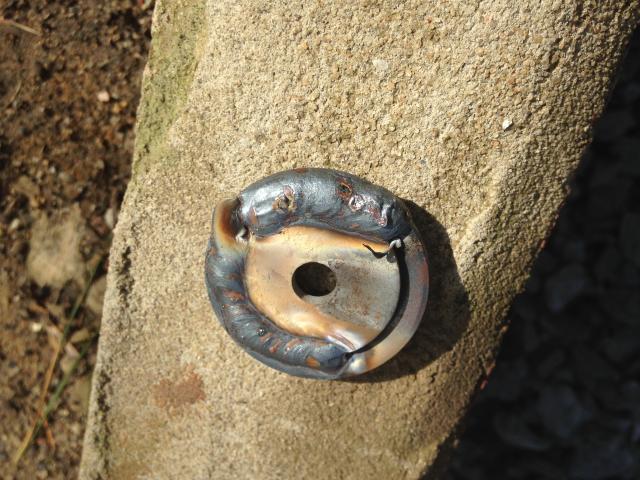
These old bolts did well, a spark hit my bare arm and you can see where I jerked LOL
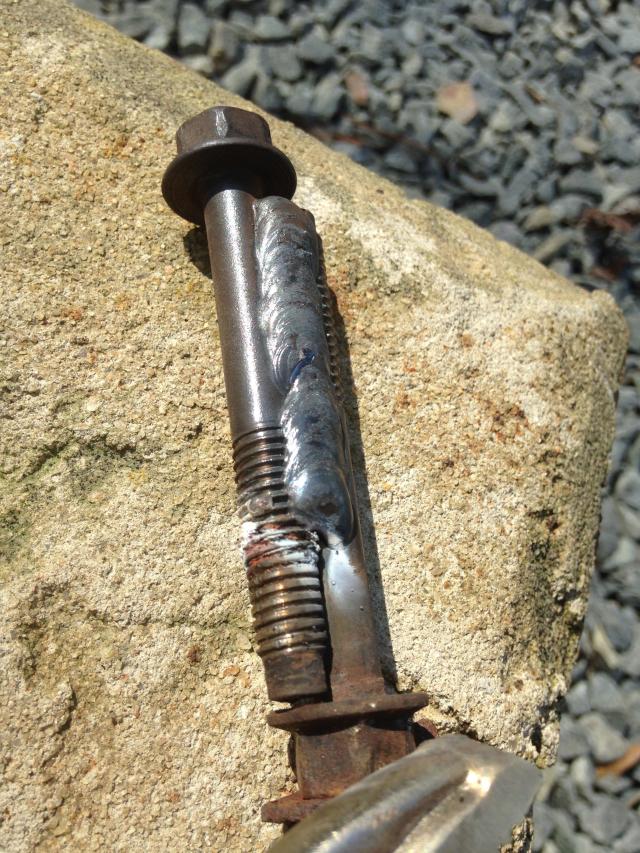
1-My thoughts:
2-It needs a lot more wire speed to look and sound good. About 30-40% more.
3-It is WAY easier to control/push the puddle. The puddle does not get in the way like with thicker wire.
4-The bead is prettier. It looks more professional, plain and simple.
5-You can move a little slower and watch it "burn in" or fuse because the puddle grows much slower.
6-Control, control, control.
7-It was hard to even try to make an undercut weld, my nemesis. It is worth using for this reason alone.
8-It did not really like my highest heat setting (140A) and tended to be more sporadic in the quality and ease of the weld. This might change on thicker steel or with more practice.
Overall, I like it and will continue to use it.
The side of these washers closer to the center was done with the .024, the other side (second pic) was with .035. Notice the thinner but much better bead on the first pic. These are small washers, the added control and smaller bead is a HUGE plus.
These old bolts did well, a spark hit my bare arm and you can see where I jerked LOL