As many of you know I purchased this camper from a board member. With the height and the tongue and rear box, it is a bit hard to open by yourself. Well I had one hand near the hinge last week and it decided to close on its own. With one torn distal tendon and surgery I am one-armed for the next 12 weeks...
So I found these campers that open the same way and have talked to the company and they have agreed to sell me the struts to assist in opening. My questions are about mounting the struts at the proper angles. It appears to be close to 45 degrees but I can not get that much on the other side of the camper because of the rounded nose.
I also have the
gas strut numbers that no one can match up other than the force which they say is 180 pounds, the top at 45 degrees is about 50 pounds measured the best I could with a scale.
So will the angle need to be close as I can get it to 45 degrees?
Will one provide enough lift or do I need to double the force if I can use two?
Can anyone decode these numbers? If I use MM it seems small for the compressed length.
Video of how they would work and pics of camper and strut below
Thank you
youtube.com
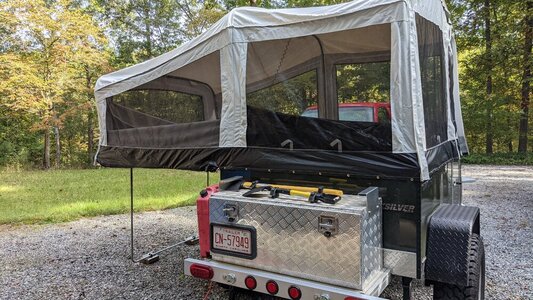
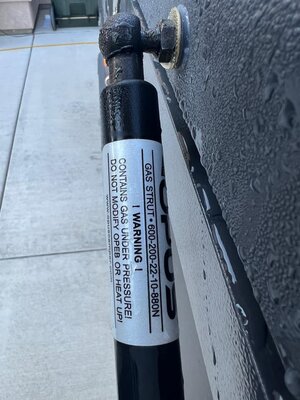
So I found these campers that open the same way and have talked to the company and they have agreed to sell me the struts to assist in opening. My questions are about mounting the struts at the proper angles. It appears to be close to 45 degrees but I can not get that much on the other side of the camper because of the rounded nose.
I also have the
So will the angle need to be close as I can get it to 45 degrees?
Will one provide enough lift or do I need to double the force if I can use two?
Can anyone decode these numbers? If I use MM it seems small for the compressed length.
Video of how they would work and pics of camper and strut below
Thank you

âï¸ demo
15 seconds · Clipped by Willcouick · Original video "OPUS OP4 Set Up Video" by Set Up Camp

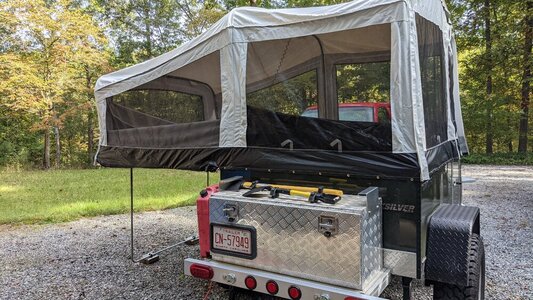
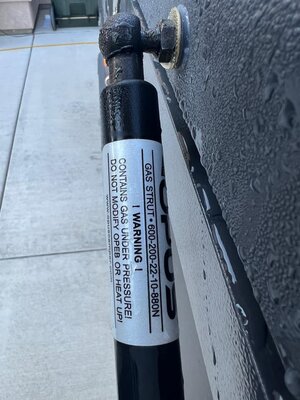
Last edited: