WARRIORWELDING
Owner opperator Of WarriorWelding LLC.
- Joined
- Jan 6, 2008
- Location
- Chillin, Hwy 64 Mocksville NC
And then.......
they where done. Did I say these guys hauled?
In less than 40 hrs, started at 7 am and they knocked off before 3 most days to beat the heat....finished.
We had to settle on door placement, and windows during the build. It was clearly on the prints but really glad the errector followed up as some changes needed to be made. Over all these guys whipped it. The insulation was spotless. I actually expected some damage going up. The over all is good....just not great. I'm detail anal and some panels just didn't square. A few oil canned. Directly from the red iron not being trued and dead square and flat across the height and length. Some trim showed the run out the worse.
After much debate I chose not to push the point. I did not like the idea of removal and adjusting. Just to many extra holes and room for a much worse end result. Over all I can live with it......just a small ulcer from my OCD.
Speaking of....me cleaning shavings off my trim for the wainscoat panel.
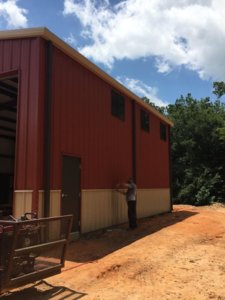
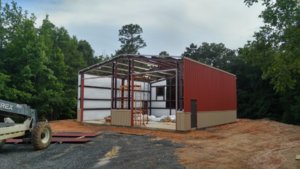
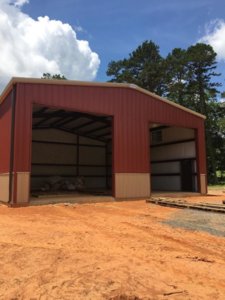
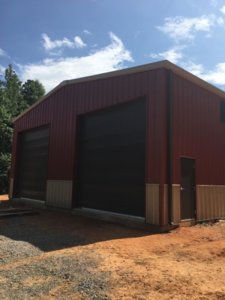
they where done. Did I say these guys hauled?
In less than 40 hrs, started at 7 am and they knocked off before 3 most days to beat the heat....finished.
We had to settle on door placement, and windows during the build. It was clearly on the prints but really glad the errector followed up as some changes needed to be made. Over all these guys whipped it. The insulation was spotless. I actually expected some damage going up. The over all is good....just not great. I'm detail anal and some panels just didn't square. A few oil canned. Directly from the red iron not being trued and dead square and flat across the height and length. Some trim showed the run out the worse.
After much debate I chose not to push the point. I did not like the idea of removal and adjusting. Just to many extra holes and room for a much worse end result. Over all I can live with it......just a small ulcer from my OCD.
Speaking of....me cleaning shavings off my trim for the wainscoat panel.
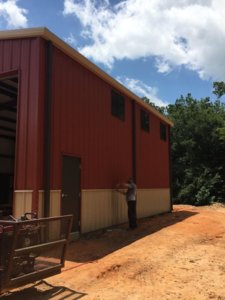