orange150
Well-Known Member
- Joined
- Mar 20, 2005
- Location
- Fairfax City, VA
Went on one last little drive and then tore into it.
I tried to combine those two videos.. for the life of me I couldn't figure it out.
It came apart really easy. Like kinda scary easy, but I guess it hadn't been on there that long.....
This is probably going to go as smooth as sandpaper
If anyone near Raleigh has the capability to make the bracket I need for the cable shifters let me know!!
I tried to combine those two videos.. for the life of me I couldn't figure it out.
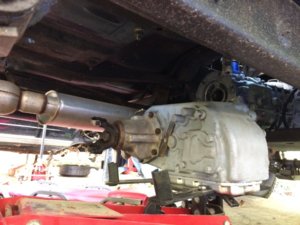
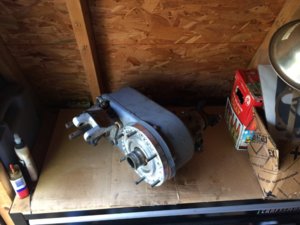
It came apart really easy. Like kinda scary easy, but I guess it hadn't been on there that long.....
This is probably going to go as smooth as sandpaper

If anyone near Raleigh has the capability to make the bracket I need for the cable shifters let me know!!