- Joined
- Mar 24, 2005
- Location
- Stanley, NC
So today Steve and I got a lot done, but don’t have much to show for it. Haha.
First we started with cleaning up.
Cleaned his 6.0 up with degreaser and pressure washer. Then we drug one of my dads th350 out and pulled the converter and drained all the oil out. Next we cleaned up Steve’s atlas.
Once everything was cleaned up, we got the chassis back up in the air and got the frame table back under it, to hold the belly at 20”.
I think the belly will eventually end up around 18” but I built the frame stand/table to be 20” to build from.
After cleaning and reorganizing and putting stuff away where it belongs, and just less clutter of parts strewn everywhere, we slid the trans and case into the belly.
this required us bolting the bent fab th350/atlas billet adapter onto the back of the 350.
next was shoe horning the 6.0 into the front of the chassis, and up onto the legs of the front of the frame table/stand.
Everything we read , says the engine has to come out the bottom, so we installed it that way.
at this point we wanted to bolt the drivetrain together and start looking at mounting it all.
I was wrong. There it is, I admit it, it’s happened before, it’ll happen again.
in my quick thinking and bench racing over the last couple weeks, I said:
“No need to change the atlas input from 32 spline to 27 spline yet, 32 is greater than 27, the atlas input should just slide over the 27 spline 350 output no issue. As long as we have the correct adapter, we can mock it up!!”
I was completely wrong!!!! It won’t go in, no matter how much wiggling and aligning you do.
next, the 350 we were using for mock up has an extra deep pan, that won’t work either. Raises the trans up too much and puts the case at a weird angle to the belly and bottom of the seat tubes.
So no more mocking up drivetrain until we get the atlas input swapped, and the a standard pan on the 350.
good news is, the 6.0 will come out of the top of the engine area, it’s tight but it fits out the top. This is without the front X tubes (35,36,37) in place.
looks like we will fab a removable front X brace so the motor can come out the top.
it was bugging me that everytime you want to pull the engine, you have to pull the front axle out.
Probably isn’t a big deal in all reality, unless changing the trans or converter would mean pulling the engine, and in turn pulling the front axle. That would be a large snowball.
at this point we started looking at link mounts and all from bent fab.
Steve purchased the modular rear link kit, which has wayyyy better geometry than the basic kit, and is the same mounts Tim @ Bent fab uses for his trailing arms.
so at that point progress on drivetrain mounting was halted, we thought we would bolt these assemblies together and tack them up ready for install.
this is when we discovered, that all Tim’s plasma cut holes are all under size. Looking at the holes, he hit several with some type of wheel, as 1/4 to 1/2 the plasma cut edge shows signs of drilling/cutting etc. However a 3/4” bolt will not fit through the holes.
This is 56 or so holes through all the tabs, brackets, and reinforcing plates need to be drilled out to 3/4 to allow the bolts to pass thru.
so we checked some more 3/8 plasma holes for the motor mount package, and half the holes are drilled for the correct size (10mm for head mounting) yet the 3/8 plasma holes barely allow a 5/16 bolt to pass thru.![]()
drilling a plasma cut hole is terrible. The plasma cutting operation leaves an oxide layer that is also hardened due to the extreme heat (45000-55000°F). This will kill a high speed steel or TiN coated HSS bit in seconds. The oxide and plasma hardened area is harder that the HSS.
Now when I cut holes on my crossfire pro table, I cut a test hole in scrap, check for bolt pass thru, and adjust my hole sizing before I cut the final part. OR I cut a .250” hole for location knowing I have to drill out larger. Typically I then use a stone wheel in a die grinder to remove just tiny amount of this hardened area and then hit with normal HSS or step bits.
Another option is to use a drill that is harder than the oxide and heat hardened area. Carbide.
So Steve went a grabbed a 3/4” masonry carbide tipped drill, chucked it up in the drill press and started drilling. I touched up the carbide to bring the OD down a little, and to increase the rake on the carbide cutting edge. It works, and makes a nice hole, but takes a lot of cutting pressure.
Going to take a while to do all 56ish remaining holes.
It’s also such a pain bc the holes are currently about the same size as the minor diameter of the 3/4” thread on the bolts. So it’s not like we have to remove a lot of material, but it’s all that oxide and hardened area.
It would be easier to take the hole from 1/8 or 1/4 up to 3/4, than what we need to do.
Steve is maybe calling Tim in the morning when cools off some haha.
I didn’t take many pictures today as I was tired and sore, and was focused on what we needed to accomplish. I’ll try to not let it happen again.
View attachment 338998View attachment 339001View attachment 339002View attachment 339003View attachment 339000
we also discovered that the poly bushings as part of the kits to mount the motor and tcase use a 1/2” bolt but have tabs with 5/8” holes.Looks like I’ll have to fire up the crossfire pro, and make new tabs for these with the correct hole sizes.
View attachment 339004View attachment 339005View attachment 339006View attachment 339007
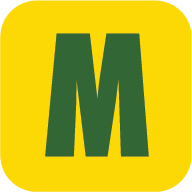
McMaster-Carr
McMaster-Carr is the complete source for your plant with over 595,000 products. 98% of products ordered ship from stock and deliver same or next day.